The Wonderful World of Floating Offshore Wind
Article - Originally posted to LinkedIn on 28.03.22
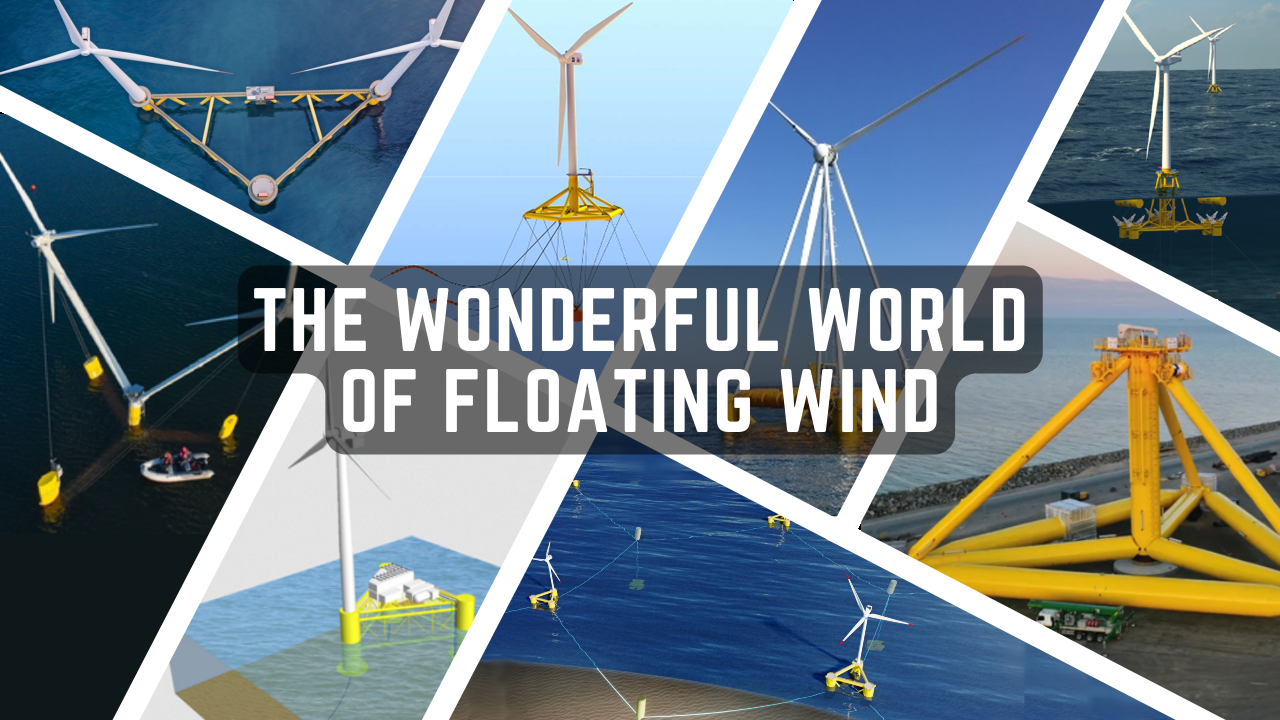
*** This article is also available in a condensed slide format, see here. ***
Floating Offshore Wind (FOW) is still very much in its infancy. As such, we are at an interesting time where many different and sometimes wacky concepts are being floated (pun intended). These will undoubtedly reduce in number as the industry matures but each design hopefully serves to better inform the next. In this article I will go through some of the less main-stream designs and concepts.
1. Basics
Before getting into the unusual designs, let’s first cover the basics. There are three parts of a FOW turbine (FOWT):
- Topside: the wind energy generator(s). This is most often the classic 3-bladed upwind horizontal axis wind turbine (HAWT).
- Foundation: the floating base on which the topside sits. There are 3 main types of floating foundations which are either buoyancy-stabilised, ballast stabilised, or mooring stabilised.
- Mooring: the components which keep the FOWT in a fixed location and may keep the platform stable. Again, 3 main types exist of taught, semi-taught, and catenary mooring.
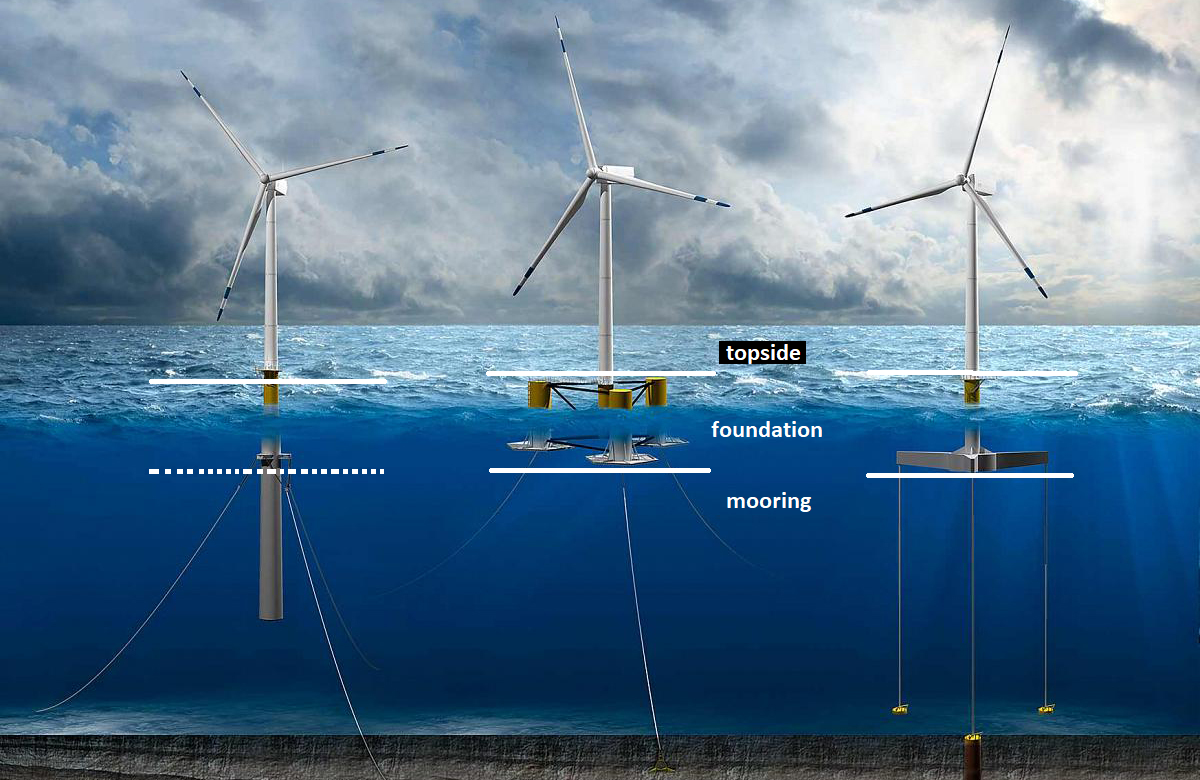
2. Topside Designs
Most FOWTs use a single 3-bladed HAWT. This makes sense when you think of FOW as a solution to water depth that is just slightly too deep for fixed-bottom wind. However, some FOW designers have taken it as a chance to rethink the topside entirely.
Trio of Doubled-Up Topsides
First up are a trio of 2-turbine floaters. The general idea is that per megawatt (MW) costs are lowered thanks to shared infrastructure. Additionally, more turbines for a designated area may be possible. I’d be very keen to see the wakes produced from two turbines so close together!
(1/3) TwinWind by Hexicon, Norway. Apparently, the platform weathervanes around a single mooring point (presumably the front of the triangle). I believe a demonstrator is under development but can’t confirm this or the scale.
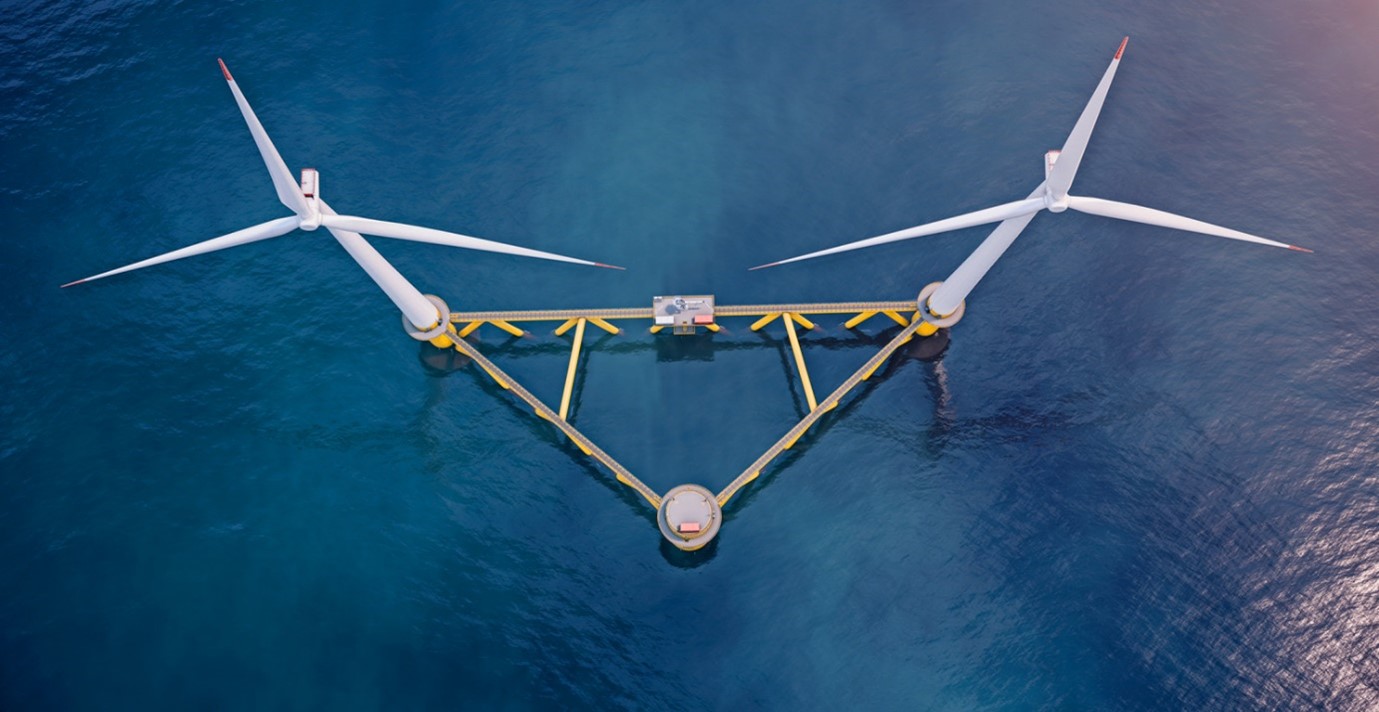
(2/3) Nezzy2 by EnBW, Germany. This design has been deployed and tested at 1:10 scale in the Baltic Sea in 2020. A full-size model was supposed to be built last year but I can’t find any updates since Nov-2020. This would be rated at 15MW (2 x 7.5MW). Note the structural tensioning wires.
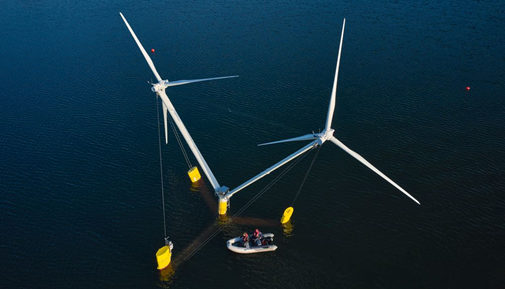
(3/3) FLOW by Flowocean, Sweden. This is another passively weathervane-ing design. It also includes a peculiar foundation design utilizing guy-lines. From what I can tell, a demonstrator is under development.
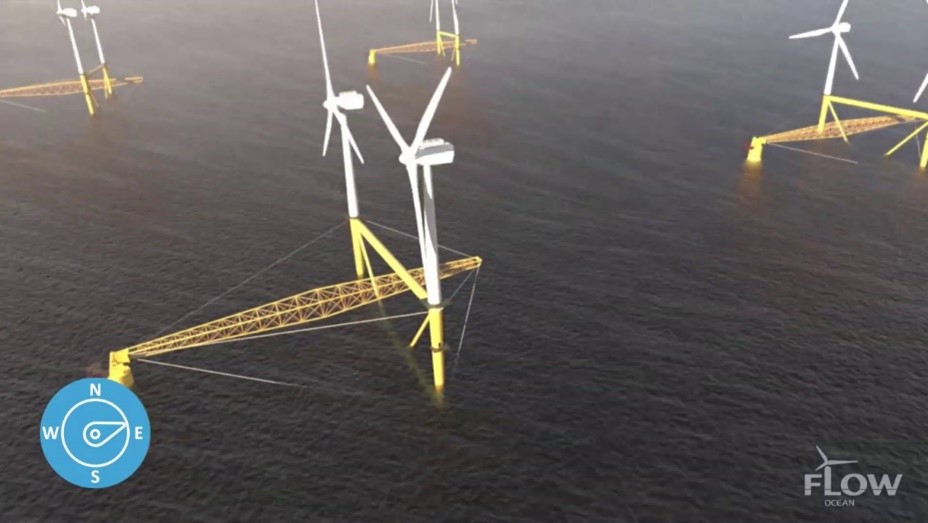
Sea Twirl
Vertical-axis wind turbines (VAWTs) for FOW seemed to be quite a popular area of research in the early 2010’s, but few examples survive today. In theory, VAWTs could be better suited to the rocking motion of FOW as they could have a lower centre of gravity due to avoiding the heavy nacelle/rotor situated at the top of the tower.
The leading FOW-VAWT is the SeaTwirl S2 by the eponymously named Swedish company. A 30kW demonstrator was deployed in 2015, the company plans a “full scale” 1MW unit for 2023. It is not clear if they intend to go larger in future or if they intent to target the small-turbine market.
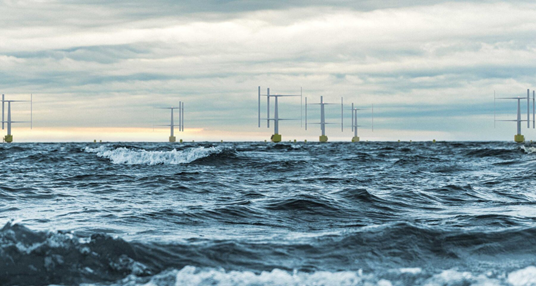
Other FOW-VAWTs which seemed to have died after promising starts are VERTIWIND and SpinFloat.
2-Bladed Downwind
In Japan, NEDO is currently operating the 3MW Hibiki demonstrator. This consists of a 2-bladed downwind turbine on top of a BW-ideol base. The idea behind 2-blades is to save weight and expense, if even the blades are slightly longer. Of course, this increases the chance of tower strikes, hence why this is a downwind rotor.
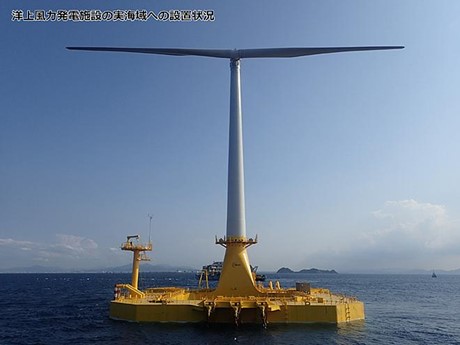
Eolink
Going further into left field, there is Eolink by a French company of the same name. Eolink claim their design saves steel, reduces interference between blades and tower, and better spreads the rotor load. Their 1:10 scale demonstrator (of a 12MW FOWT) is shown below in 2018. From what I gather, a 5MW demonstrator was supposed to be deployed in 2020, but I can’t find anything confirming if it came to fruition. They say a off-the-shelf generators/rotors in the range of 5-13MW would only need a “front transition piece” fitted to be suitable for their system. Beyond this, and up to the 20MW envisioned, modifications would be necessary to better leverage the 4-mast system.
Quite frankly, some of the numbers suggested on the company’s website regarding LCOE and deployment numbers seem a bit far-fetched, but I am quite fond of their design.
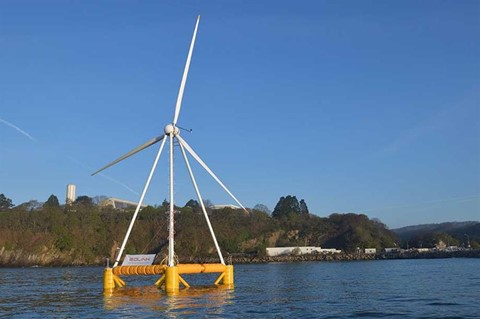
3. Foundations
Foundations are probably the most interesting research topic of the 3 components. Contrary to the previous section, many designs assume that unaltered wind turbines suitable for fixed-bottom structures will be used for FOW. This is to keep overall costs down. The topic of FOW design is then really the design of floating foundations and mooring which can keep the WT as stable as possible. The popular foundations of today achieve this by using relatively large and heavy steel and/or concrete structures which borrow heavily from Oil & Gas. These designs are expected to be refined to reduce material usage and, hence, costs. Parallel to this, a new and innovative batch of foundation designs are emerging which I have seen dubbed “advanced” and “next generation” foundations. These are the focus of this section with the Gazelle, TetraSpar, and HexaFloat concepts.
Gazelle
Gazelle Wind Power have been a bit secretive about their foundation design making it difficult to tell how it operates. It looks like there are 6 arms, 3 above the water and 3 below. The 3 submerged arms look like they provide some buoyancy/ballast and also appear to suspend a counterweight between them. It is not clear what role the 3 above-water arms perform. Gazelle make the usual claims about saving steel and better performance. Regardless, the design is a definite departure from O&G platforms. Gazelle have a 2MW demonstrator planned for 2023 in the Canary Islands.
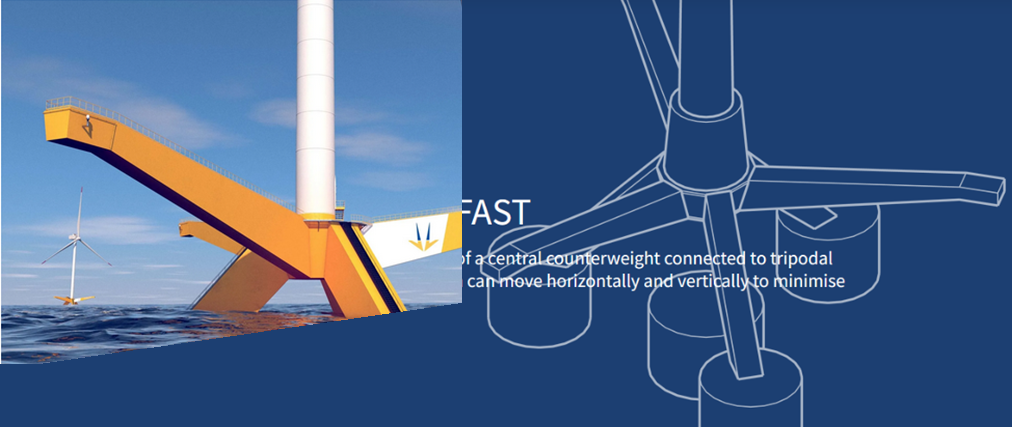
TetraSpar
TetraSpar is a personal favourite of mine. This foundation design includes a triangular keel structure (in red) suspended from the floating structure. TetraSpar have designed their foundation for manufacturability, all members are fairly simple and bolt together at assembly, hence avoiding welding. A 3.6MW demonstrator is currently running in Norway. Great set of pictures of the assembly can be found here.
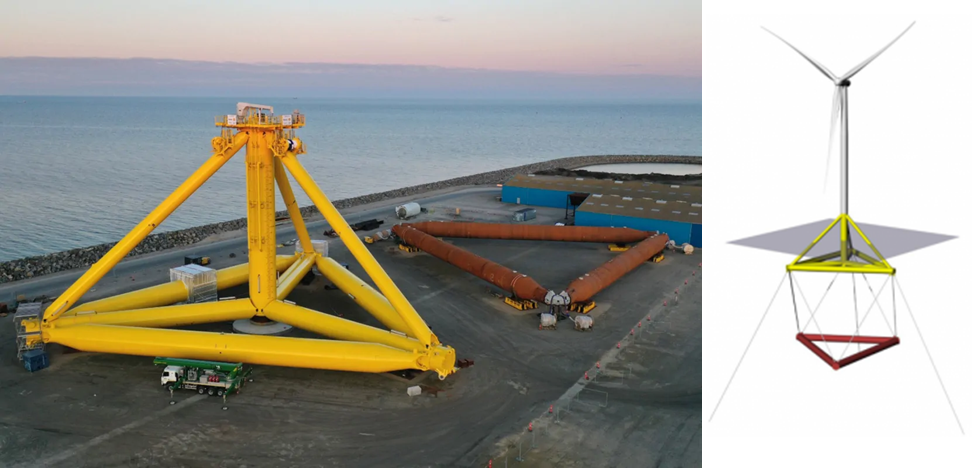
HexaFloat
HexaFloat, by Saipem, looks slightly like a mash up of Gazelle and TetraSpar. A “pendulum” is hung from the floating foundation. A demonstrator is due to be deployed in Ireland in 2022, but not much has been said for a few years now.
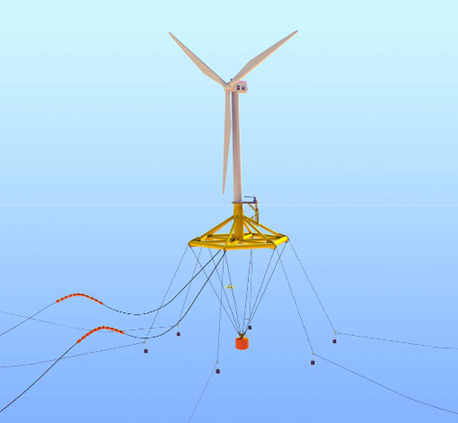
4. Moorings
The final part of a floating wind design is the mooring. I will concentrate on the mooring lines themselves at not their anchoring to the seabed. Right now, a lot of attention in this topic is being paid to material development such namely synthetic rope. This is to move away from traditional chains. However, many are also looking at different arrangements of moorings and trying to find better solutions than simple catenary or taught moorings. This includes “multi-segmented” mooring which can combine catenary chains and taught ropes together, perhaps even using buoys as well.
All things considered, this topic is more iterative than innovative and there is only one solution to discuss which takes an altogether different approach. This is the shared mooring concept of Honeymoorings.
Honeymoorings Solution
Total Energies have recently announced their development of a honeycomb-inspired shared mooring solution. As usual, there isn’t much to go on but one imagines that this reduces the number of anchors and, if done right, CAPEX and OPEX costs. Presumably the system also makes for easier installation once the FOWT is towed to site.
Being speculative, this design is perhaps better suited for deep waters where the risk of moorings sagging and dragging on the seabed is reduced. Additionally, deeper water would require more moorings and anchoring inspections would be more costly, hence this system becomes more viable.
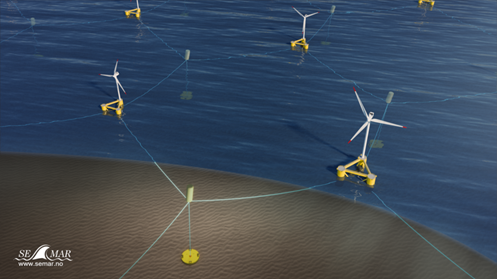
5. Bonus Concepts
There are some other interesting designs regarding floating wind which don’t fit into the categories of topside/foundation/mooring. Here are 4 very active projects.
Self-Erecting Turbine
SENSEWind are a UK company making self-erecting rotors. Whilst this technology is applicable to onshore and fixed-bottom offshore, floating wind will have particularly struggle with crane lifts. Given the inherently deeper water of floating wind, few crane vessels, if any, will be able to jack-up off the sea floor and be able to manage the heavy-lift and high heights of modern WTs, hence more specialised (read: expensive) vessels will be required. Having rotors which “crawl” down to near water level would allow for a far wider range of vessels to be used. The picture below regards a BEIS funded demonstrator announced this January (2022).
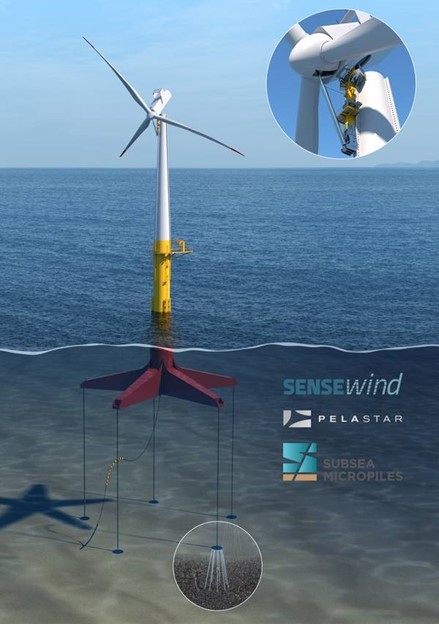
FOW + Wave Energy
Marine Power Systems appointed Black and Veatch to design a combined FOWT and wave generator in November 2021. In theory you have two energy generators sharing infrastructure so the cost should be lower overall. This is an interesting project to watch as typical floating foundations aim to reduce the influence of waves on the topside as much as possible, never mind harnessing energy at the same time. [Full disclosure, I used to work for B&V, they’re a lovely bunch of people]
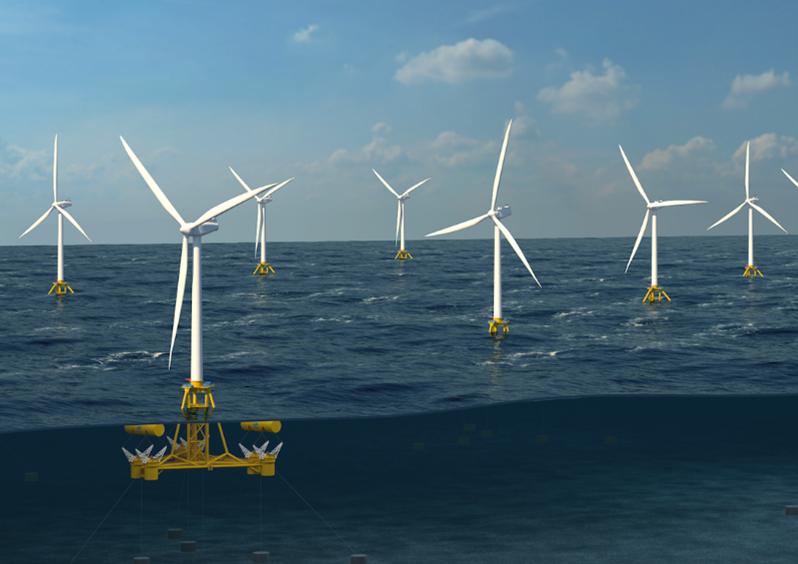
FOW + Hydrogen
ERM’s Dolphyn project (Deepwater Offshore Local Production of HYdrogeN) combines FOW with energy storage via an on-board hydrogen electrolyser. In other words, this is decentralised offshore hydrogen production. This is a fascinating topic and one which I am, frankly, under-read on but would like to study more. To be economically viable, this concept must be better than either centralised-offshore or centralised-onshore hydrogen production. Considering offshore, this requires that, for some distance from shore and/or quantity of energy, it becomes more effective to pipe energy as hydrogen than transmit it as electricity. The other main consideration I see is the cost difference of having a FOWT with a deck suitable to house the electrolyser, as opposed to one without (such as a spar-type).
Aside from the many engineering aspects, the project is also fascinating for the pace it's developing. In 2020, it was announced that a 2MW demonstrator (unclear if that refers to both the WT and the electrolyser) was planned of Aberdeen circa “early-mid 2020s” and a 10MW pre-commercial unit sometime after that. A year later, the demonstrator idea was scrapped in favour of going straight to the 10MW pre-commercial unit. And, just this month (March 2022), it was announced that a GW-sized farm is now planned for the Pembrokeshire coast with the company Source Energie. This is an impressive confidence in the concept given that not even a demonstrator exists yet.
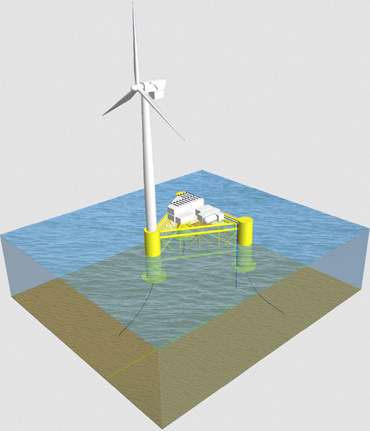
Wind Catching System
For the final concept of the article, I present to you the Wind Catching System by the Norwegian company of the same name. The concept consists of a wall of 126 turbines (so I’m told, I haven’t counted) rated at 1MW. However, it’s stated these are smaller than usual at rotor diameters c. 30m, whilst a typical 1MW HAWT is c. 50m. I also get the impression that these WTs don’t pitch. Despite quite a few claims on the company website, there is, unfortunately, very little information on this system. I remain highly sceptical of the design until more details are released. For now, my take is that, at worst, the physics don’t add up for this design, at best, this would be a power regulation nightmare.
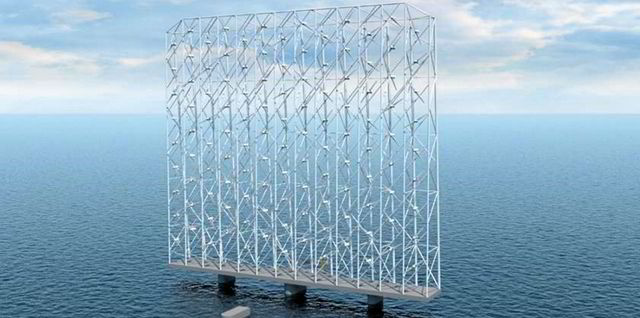
6. Conclusion
The Floating Offshore Wind design space is full of different concepts and approaches to the myriad of challenges inherent to floating wind. As with any new field, many concepts will not make it past the demonstrator stage but they will help inform the next generation of concepts. In this article I have tried to collect some of the more exotic ideas, time will tell if they survive. For now, engineers and scientists can take inspiration from their creative thinking.
If you enjoyed this article, please give it a like (or even a share!), it really helps improve its reach. If there's anything incorrect or links aren't working, please let me know as well. Rory.
------------------------------------------------------------------
I am a PhD student at Glasgow University. My PhD is in the application of Machine Learning for offshore wind turbines. More specifically, I am researching the convergence of ML, Digital Twins, and floating wind turbines. If you have access to resources which you think might be useful (e.g. datasets, contacts to FOWT designers/operators/developers, wind industry contacts who practice Digital Twins), I would be more than appreciative if you got in touch.
Follow on Twitter